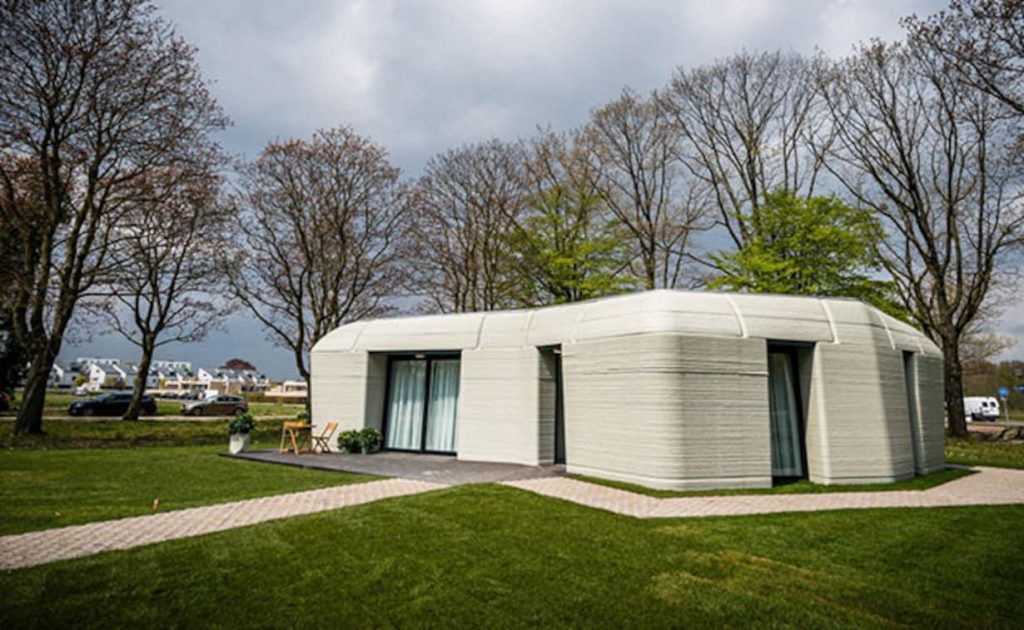
Additive manufacturing, also known as 3D house printing, is gaining popularity among manufacturers. Currently, digital models of buildings are being transferred to the construction industry, where 3D printers are used to erect structures. By extruding a concrete mixture layer by layer along the limited contour of the building’s structure, building structures are created or the building is “printed.” Even though there is an increasing demand for 3D printed houses as a result of the groundbreaking benefits it offers, there are some crucial factors that create doubts in our minds as to whether or not to go ahead with 3D house printing.
3D Printing Can’t Do Everything
Simply, 3D printers produce the structure, one of the many components of a house. The foundation and walls can be 3D printed, but pipes, wires, and other installations cannot. 3D house printers cannot be used to paint walls or furnish a kitchen. To incorporate plumbing, heating and cooling, electrical, roofing, interior finishing, furnishing, landscaping, etc., you must still coordinate the various trades. Even 3D-printed walls often appear rough and unfinished, necessitating post-processing similar to conventional construction. Consequently, when not only the 3D-printed framework but also the labor and monetary cost of all the additional components are considered, the actual savings are typically much less than anticipated. The value of a home exceeds the cost of the walls and foundation by multiples, after all.
Lack Of Engineering For The Amount Of Commercialization And Marketing
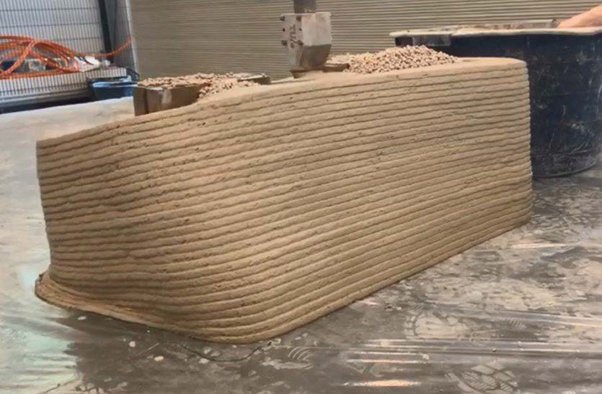
It is difficult to emphasize enough that 3D house printing is a clearly experimental technology, despite the fact that companies are building homes for their clients. Because of the lack of time to undertake thorough testing, independent scrutiny, and peer review, the outcomes are always subpar. Similar to the medical device industry, the construction industry is conservative and does not foster this type of innovation. However, in contrast to the medical device industry, you are free to live in an untested home and incur all liability.
Accounting Can be Shady
Beyond the engineering concerns, the rapidity with which a 3D house is completed casts major doubt on the budgetary promises made, and we can determine that some of them are simply white lies based on their timing. Because the technology and materials are experimental and not adequately cost-accounted for, most enterprises must be inventive when claiming expenses linked with home construction, opting not to include operations and R&D costs for an unfinished product. Despite the fact that 3D house printing companies have a great deal of room to manipulate the figures, cost estimates for building a home have been consistently revised upwards, Researchers have seen as low as a 20% reduction in construction costs claimed.
Problems With Reinforcing 3D Printed Concrete Structures

As durable as concrete is in most applications, it requires reinforcement to prevent cracking over time. The physical and mechanical qualities of concrete are highly durable in a compact form, but its tensile strength is compromised when it is extended across a vast region. This is when reinforcing rebar comes into play – for reinforcement. How can the labor-intensive task of installing rebar be combined with the automation of 3D printing? This is currently one of the greatest challenges. This is currently one of the greatest challenges. How can 3D-printed concrete be successfully and efficiently reinforced? As a result, a technology gap must be bridged before a totally automated 3D printing method can produce larger, multistory structures.
Hidden Costs
Certain media efforts have been rather dishonest about the total price of 3D-printed houses. In their cost forecasts, they omit the less obvious but equally significant hidden costs of transporting and maintaining the machinery. Transporting large-scale 3D printers can cost thousands of dollars. The coarse and heavy nature of the substance they work with will necessitate a tremendous deal of wear and tear once they begin producing greater quantities. Consequently, you will want technical skills on-site. Not only programmers but also tradespeople who can repair and replace mechanical components. Consider these forecasts with a grain of salt when you hear marketing efforts for houses built with 3D printers claiming “a house will cost $10,000 to construct.”
Conclusion
That being said, 3D-printed buildings have a lot of promise as “expeditionary structures” for things like disaster relief, military operations, emergency repairs, or space exploration. All a printed structure needs are the machine and some raw materials, so the planning and logistics are easy. But when you have an established supply chain and a lot of time to plan, you can mass-produce standardized parts at a factory off-site that are cheaper and of better quality.
[…] 5 Reasons Why You Should Not Go Ahead With 3D House Printing […]